

1) ÆíÀǼº

¾Æ¿¬À» ÀÌ¿ëÇÏ´Â Àü·¡ÀÇ ¿ëÀ¶¾Æ¿¬ÇǸ·Ã³¸®¿Í Zinga ÀÇ ÁÖ¿äÇÑ Â÷ÀÌÁ¡Àº Zinga ´Â ´©±¸³ª ½±°Ô ¹Ù¸¦
¼ö ÀÖ´Ù´Â Á¡ÀÔ´Ï´Ù. ±×·¯¸é¼µµ ¿ëÀ¶¾Æ¿¬ ÇǸ·Ã³¸®¿Í ¶È°°Àº Èñ»ýºÎ½Ä¿¡ ÀÇÇÑ ºÎ½Ä¹æÁö ¼º´ÉÀ» °¡Áø Zinga
ÇǸ·À» Çü¼ºÇÒ ¼ö ÀÖ½À´Ï´Ù
( Real Zinganisation )
2) ½À±âÇã¿ë¼º

Zinga ´Â ½À±â°¡ ÀÖ´Â ¸é¿¡µµ µµÆ÷ÇÒ ¼ö ÀÖ´Â ÀÌÁ¡ÀÌ ÀÖÀ¸¸ç ÀÌ ¶§ Zinga ÀÇ ¼º´É¿¡ ¹®Á¦°¡
¾ø½À´Ï´Ù. ÀÌ¿¡ ´ëÇØ ¾î¶°ÇÑ ¿ø¸®·Î ½À±â°¡ Zinga ¿¡ ¿µÇâÀ» ÁÖÁö ¾Ê´ÂÁö¿¡ ´ëÇÑ ¿¬±¸°¡ ÀÖ¾ú½À´Ï´Ù.
±Ý¼ÓÀÇ °ÅÄ£ Ç¥¸é¿¡ ³²¾ÆÀÖ´Â ¹°À» Zinga °¡ ¹Ð¾î³»¸ç Á¢ÂøÀ» ÇÏ°Ô µË´Ï´Ù. ÀÌ·¯ÇÑ ÀåÁ¡Àº ½ÇÁ¦ÀûÀ¸·Î
Zinga ¸¦ °á·Î°¡ ÀϾî
³ª´Â ºÎÀ§¿¡ »ç¿ëÇÒ ¼ö ÀÖ´Ù´Â °ÍÀ» ÀǹÌÇÕ´Ï´Ù.
3) ¾Æ¿¬µµ±Ý¸é À§¿¡ µµÆ÷ °¡´É

Zinga ´Â ´Ù¸¥ ¸ÞÅ»¶óÀÌ¡ÀÌ µÈ Ç¥¸é ¹× ¾Æ¿¬ÇǸ·Ã³¸®µÈ Ç¥¸éÀÇ ¼Õ»óµÈ ºÎÀ§¿¡ »ç¿ëÇÒ ¼ö ÀÖ½À´Ï´Ù.
¿ëÀ¶¾Æ¿¬µµ±Ý¸é¿¡ Zinga ¸¦ µµÆ÷ÇÏ¿©µµ ¹Ú¸®°¡ ÀϾÁö ¾Ê½À
´Ï´Ù.
4) ¾ö°ÝÇÏÁö ¾ÊÀº Ç¥¸é󸮿ä°Ç

Zinga ÀÇ µµÆ÷ Àü »÷µåºê¶ó½ºÆ®´Â ¹Ýµå½Ã ÇÊ¿äÇÑ °ÍÀº ¾Æ´Õ´Ï´Ù. (»÷µåºê¶ó½ºÆ®¸¦ ÇÔÀ¸·Î¼ ÃÖÀûÀÇ Àü±âÈÇÐÀû
ºÎ½Ä¹æÁö È¿°ú¸¦ ¾òÀ» ¼ö´Â ÀÖÁö¸¸).
öºê·¯½¬·Î À̹°ÁúÀ» Àß Á¦°ÅÇÏ°í µµÆ÷Çϸé ÃæºÐÇϸç ÀÌ·Î½á ±âÀç¿¡ ´Ü´ÜÈ÷ Á¢ÂøÀÌ
µÇ¾î ºÎ½Ä¹æÁö ±â´ÉÀ» ¼öÇàÇÏ°Ô µË´Ï´Ù.
»÷µåºê¶ó½ºÆ®, Å»ÁöÀÛ¾÷Àº ±âÁ¸ÀÇ ÆäÀÎÆ®°¡ ³²¾ÆÀְųª, ±×¸®½º³ª ¿ÀÀÏ, ³ì, ¿°ºÐ,
¶Ç´Â »êÀÌ ¹¯¾î ÀÖ´Â °æ¿ì¿¡´Â ÇÊ¿äÇÕ´Ï´Ù.
5) ÀçµµÆ÷ ¹× Touch-Up º¸¼öÀÇ ¿ëÀ̼º

¾Æ¿¬¼ººÐÀÌ ¸ðµÎ ¼ÒÁøµÈ ÈÄ¿¡ Áï ±Ý¼ÓÇ¥¸é¿¡ ÀüÇØÁú ¼ººÐÀ¸·Î¼ÀÇ ¾Æ¿¬ÀÌ ¾ø¾îÁø ´ÙÀ½¿¡´Â Zinga ´Â Ç¥¸éó¸®
µîÀÇ ºñ¿ëÀ» µéÀÌÁö ¾Ê°í °ð¹Ù·Î ÀçµµÀå ¶Ç´Â Touch-Up ÄÚÆÃÇÒ ¼ö ÀÖ´Â, ´Ù¸¥ ÄÚÆÃÁ¦¿¡¼ º¼ ¼ö ¾ø´Â
ÀÌ·ÊÀûÀÎ ÀåÁ¡ÀÌ ÀÖ½À´Ï´Ù. ÀÌ ¶§ »õ·Î µµÆ÷ÇÑ Zinga ´Â ±âÁ¸ÀÇ Zinga ¿Í ¿ÏÀüÈ÷ À¶ÇÕÇÏ¿© ÀÏüÀÇ
ÇǸ·À» Çü¼ºÇÏ´Â µ¶Æ¯ÇÑ ¼ºÁúÀÌ ÀÖ½À´Ï´Ù. ±âÁ¸ÀÇ ¾Æ¿¬µµ±ÝÀº ÀçµµÀåÀÇ °æ¿ì ±âÁ¸ÀÇ Ãþ°úÀÇ Á¢Âø·Â¿¡ ¹®Á¦°¡
ÀÖ½À´Ï´Ù. Zinga ´Â ÀÌ·± ¹®Á¦°¡ ¾øÀ¸¸ç ±âÁ¸ ÇǸ·°ú ´Ü´ÜÈ÷ Á¢ÂøÀÌ µË´Ï´Ù.
Zinga ´Â ³ìÀÌ ¾à°£ ½¼ ¸é, ½À±â°¡ ÀÖ´Â ¸é¿¡ µµÆ÷ÇÒ ¼ö ÀÖÀ¸¹Ç·Î º¸¼öÇÒ ºÎºÐÀÇ Ç¥¸é󸮴 ¸Å¿ì
°£´ÜÇÕ´Ï´Ù. ¹°·Î ¾Æ¿¬¿° (Zinc Salt) À» Á¦°Å ÈÄ Zinga ¸¦ µµÆ÷ÇÕ´Ï´Ù. ÀÌ´Â ¸¹Àº Àη°ú
ºñ¿ëÀ» Àý°¨ÇÒ ¼ö ÀÖ´Â Zinga ¸¸ÀÇ ÀåÁ¡ÀÔ´Ï´Ù.
6) ÀÛ¾÷¹°ÀÇ º¯Çü ¿ì·Á ¹«

¿ëÀ¶¾Æ¿¬µµ±Ý°ú ºñ±³ÇÏ¿© ¶Ç ÇϳªÀÇ Áß¿äÇÑ ¹®Á¦´Â ÀÛ¾÷¹°ÀÌ µµ±ÝÁ¶¿¡¼ ³ôÀº ¿Âµµ ¹× ÀÀ·ÂÀ¸·Î º¯ÇüÀÌ µÉ ¼ö
ÀÖ´Ù´Â Á¡ÀÔ´Ï´Ù. Á¶¸³½Ã¿¡ Ä¡¼ö º¯ÇüµÈ ºÎǰÀº ¹®Á¦°¡ µÉ ¼ö ÀÖ½À´Ï´Ù Zinga ´Â ÀÌ·± ¹®Á¦¸¦ ¼ö¹ÝÇÏÁö
¾Ê½À´Ï´Ù.
7) Å©·¢ÀÇ ¹ß»ý °¡´É¼º ¹« - Zinga ÇǸ·ÀÇ À¯¿¬¼º

¿ëÀ¶¾Æ¿¬µµ±Ý½Ã »ý¼ºµÇ´Â ö-¾Æ¿¬ ÇÕ±ÝÀº ¾Æ·¡ÀÇ ¸ðÀ纸´Ù °æµµ°¡ ³ô½À´Ï´Ù.
( Brinel °æµµ ; ö - 159 DPN, µ¨Å¸Ãþ - 179 DPN, °¨¸¶Ãþ - 244 DPN )
ÀÌ´Â Àüü ¾Æ¿¬µµ±ÝÃþ¿¡ Ã뼺À» ÁÖ¾î Å©·¢ÀÌ ¹ß»ýÇϱ⠽±°Ô ¸¸µå´Âµ¥ ½Ã°£ÀÌ È带¼ö·Ï Å©·¢ÀÇ
¹ß»ý °¡´É¼ºÀº ³ô½À´Ï´Ù.
Zinga ´Â ±âÀçÀÇ ¿¿¡ ÀÇÇÑ ¼öÃàÆØÃ¢¿¡ ¼Õ»óÀ» ¹ÞÁö ¾Ê°í ºÎ½Ä¹æÁö ±â´ÉÀ» ¹ßÈÖÇÕ´Ï´Ù. Zinga
´Â ±âÀçÀÇ ±â°èÀûÀÎ º¯Çü¿¡ ¼Õ»óÀ» ¹ÞÁö ¾Ê½À´Ï´Ù.
8) Â÷ÆóÇǸ·¿¡ ÀÇÇÑ º¸È£

ÀÌ·¯ÇÑ ºÎ½Ä¹æÁö ¿ø¸®´Â ¿ëÀ¶¾Æ¿¬µµ±Ý¸·ÀÇ Ç¥¸éº¸È£±â´É°ú ¶È °°½À´Ï´Ù. ÃÖÃÊ¿¡´Â Zinga ÃþÀÌ ´Ù°ø¼ºÀ̹ǷÎ
½À±â¿Í »ê¼ÒÀÇ ¿µÇâÀ¸·Î °è¼Ó °æÈ°¡ µË´Ï´Ù ( Cementation ). ±× °úÁ¤¿¡¼ Zinc Salt
ÃþÀÌ »ý¼ºµÇ°í, ÀÌ Zinc Salt ÃþÀÌ °¢ ¾Æ¿¬ºÐ¸»À» µÑ·¯½Î°Ô µÇ¾î ±â°øÀ» ¸Þ¿ö³ª°¡¸ç ÁÖº¯ ´ë±â·ÎºÎÅÍ
Zinga ÃþÀ» Â÷´ÜÇÏ´Â ±â´ÉÀ» ÇÕ´Ï´Ù. ÀÌ·¯ÇÑ °úÁ¤Àº Zinga ÃþÀÇ ¸Ç À§ ºÎºÐ¿¡¼ ½ÃÀÛÇÏ¿© ÀÏÁ¤ÇÑ
±íÀÌ¿¡ µµ´ÞÇÏ´Â µ¿¾È °è¼ÓµË´Ï´Ù.
À̶§ »ý¼ºµÇ´Â Â÷´ÜÇǸ·ÀÌ Zinga ÇǸ·³»ºÎ·ÎÀÇ ½À±âÀÇ È®»ê ¹× ¿À¿°¹°ÁúÀÇ Ä§Åõ¸¦ ÀúÁöÇÕ´Ï´Ù. µû¶ó¼
Zinga ÇǸ·ÀÇ ¸Ç »óºÎ¿¡ Àִ Ȱµ¿¼ºÀÇ ( Active ) ¾Æ¿¬ ºÐ¸»Àº Zinc Salt ÈÇÏ¿© ÀÚ¿¬È÷
Èñ»ýºÎ½ÄÀÇ ±â´ÉÀ» ÀÒ¾î¹ö¸®°Ô µË´Ï´Ù. ±×·¯³ª ÀÌ »õ·ÎÀÌ Çü¼ºµÈ Zinc Salt ÃþÀº Â÷ÆóÇǸ· ±â´ÉÀ» ÇÕ´Ï´Ù.
ÀÌ ´Ü°è¿¡¼ Zinga ÀÇ »óºÎ Zinc Salt ÃþÀº °í¾Æ¿¬¸» µµ·áÀÇ ±â´ÉÀ» Çϸç, ÀÌ °æÈµÈ ÃþÀº
¾Æ·¡ÀÇ Èñ»ýºÎ½Ä ±â´ÉÀ» Çϴ Ȱ¼ºÀÇ ¾Æ¿¬ºÐ¸»ÃþÀ» º¸È£ÇÏ°Ô µË´Ï´Ù. »Ó¸¸ ¾Æ´Ï¶ó ÀÌ·¸°Ô °æÈµÈ
Zinc Salt ÃþÀº ±â°èÀûÀÎ Ãæ°Ý¿¡ ¸Å¿ì °ÇÑ ³»Ãæ°Ý¼ºÀ» °¡Áö°Ô µË´Ï´Ù.
9) ¼ö¸í- ³»½Ä¼º

Zinga ´Â °°Àº µÎ²², °°Àº ÀϹÝÀû ¼øÇÑ »ç¿ëÁ¶°Ç ÇÏ¿¡¼ ³»±¸¼º¿¡ ÀÖ¾î¼ ¿ëÀ¶¾Æ¿¬µµ±Ý°ú À¯»çÇÕ´Ï´Ù.
( Report ÂüÁ¶ ) ¾Æ¿¬ºÐ¸»ÀÌ ¸ðµÎ ¼ÒÁøµÇ±â Àü¿¡´Â ³ìÀÌ ÇÇÁö ¾Ê°í ¾Æ¿¬ºÐ¸»ÀÌ ¿ÏÀüÈ÷ ¾ø¾îÁø ºÎºÐ¿¡
±¹ÇÑÇÏ¿© ³ìÀÌ ¹ß»ýÇÕ´Ï´Ù.
±×·¯³ª ºÎ½Ä¼ºÀÌ °ÇÑ ºÐÀ§±â ÇÏ¿¡¼´Â Zinga ´Â ¿ëÀ¶¾Æ¿¬µµ±Ý¿¡ ºñ°ßÇÒ ¼ö ¾ø´Â
³»½Ä¼ºÀ» º¸¿©ÁÝ´Ï´Ù.

- ¿°¼öºÐ¹«Å×½ºÆ® ; °¢ ±¹¿¡¼ÀÇ Å×½ºÆ® °á°ú Zinga ´Â ÃÖ¼Ò 5 ¹è ÀÌ»óÀÇ Æ¯¼º
( Singapore, Taiwan, Belgium, Bangladeshi °¢±¹ Å×½ºÆ® )

- »ê¿ë¾× ; pH 6.0 ¡¾ 0.2 ÀÇ ¿ë¾×¿¡ ħ¼öÅ×½ºÆ®¿¡¼ Zinga ´Â 3 ¹è ÀÌ»óÀÇ ³»ºÎ½Ä
¼º ( BNF Fulmer, UK )

- ¾ËÄ®¸®¿ë¾× ; pH 11.5 ÀÇ °»³»¼ö¿¡¼´Â ¿ëÀ¶¾Æ¿¬µµ±ÝÇÑ Water Pump °¡ 6 °³¿ù ¸¸
¿¡ ³ìÀÌ ½¼ µ¥ ºñÇØ Zinga ´Â µµÆ÷ ( 1996 ) ÈÄ 5 ³âÀÌ Áö³ ÇöÀç±îÁö ³ì¹ß»ý¾ø
ÀÌ »ç¿ëÇϰí ÀÖ½À´Ï´Ù. ( Val Reefs Gold Mine of South Africa )
¿ëÀ¶¾Æ¿¬µµ±Ý¸é
À§¿¡ ZINGA ÀÇ µµÆ÷
1.3.1. ºÎ½Ä¹æÁö ¼º´ÉÀÇ ¹è°¡
Taiwan ÀÇ National Cheng Kung University ( ÏÐØ¡à÷ÍíÓÞùÊ ) ¿¡¼´Â Zinga
¸¦ ¿ëÀ¶¾Æ¿¬µµ±Ý¸é À§¿¡ µµÆ÷ÇÏ¿© ¿°¼öºÐ¹«½ÃÇè ( Salt Spray Test ; ASTM B 117-94
) À»
ÇÏ¿´½À´Ï´Ù.
- ¿ëÀ¶¾Æ¿¬µµ±Ý À§¿¡ 60 ¥ìm ÀÇ Zinga µµÆ÷ - 6,000 ½Ã°£ Åë°ú ( ³ì¹ß»ý ¹« )
- ³ª±Ý¼Ó À§¿¡ 120 ¥ìm ÀÇ Zinga µµÆ÷ - 6,000 ½Ã°£ Åë°ú ( ³ì¹ß»ý ¹« )
À§ÀÇ ½ÇÇè¿¡ ÀÇÇÏ¸é ¿ëÀ¶¾Æ¿¬µµ±Ý À§¿¡ 60 ¥ìm ÀÇ Zinga ¸¦ µµÆ÷Çϸé ÄÚÆÃÇǸ·ÀÇ ¼ö¸íÀÌ Zinga
µµÆ÷°¡ ¾ÈµÈ ¿ëÀ¶¾Æ¿¬µµ±Ýº¸´Ù 20 ¹è ÀÌ»ó Áõ°¡ÇÏ¿´½À´Ï´Ù.
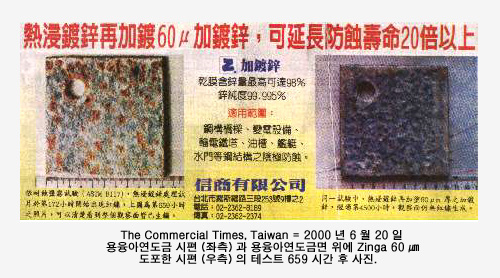
¿ëÀ¶¾Æ¿¬µµ±ÝµÈ ½ÃÆíÀº ¿°¼öºÐ¹«½ÃÇè ( ASTM B117 ) 172 ½Ã°£ ÈÄ¿¡ ³ìÀÌ ¹ß»ýÇϱ⠽ÃÀÛÇÏ¿´À¸³ª,
µ¿ÀÏÇÑ ¿ëÀ¶¾Æ¿¬ µµ±Ý¸é À§¿¡ 60 ¥ìm ÀÇ Zinga ¸¦ µµÆ÷ÇÑ ½ÃÆíÀº 4500 ½Ã°£ ÈÄ¿¡µµ ³ì ¹ß»ýÀÌ
Àü¹«ÇÏ¿´½À´Ï´Ù.
¿ëÀ¶¾Æ¿¬µµ±Ý°ú
Zinga ÀÇ ÇǸ·ºñ±³
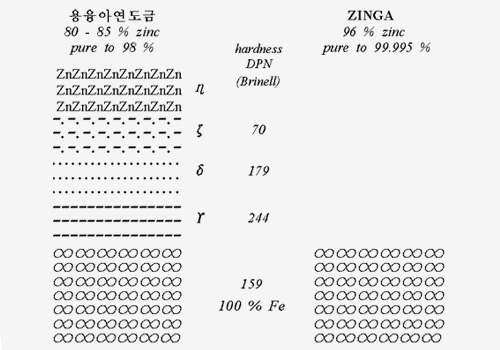
Zinga¿Í
¿ëÀ¶¾Æ¿¬µµ±ÝÀÇ ºñ±³
 |
Ç׸ñ |
ZINGA
|
¿ëÀ¶¾Æ¿¬µµ±Ý |
ºÎ½Ä¹æÁö ÇüÅÂ
|
Active
( Ȱ¼º, ¹ÝÀÀ¼º )
+ Passive ( ºñȰ¼º, ºÎµ¿Å )
|
Active
Protection
( Ȱ¼º, ¹ÝÀÀ¼º ) |
¿°¼öºÐ¹«½ÃÇè
Å×½ºÆ® ³²¾Æ°ø Ç¥Áؽɻ籹(Áß·®¼Õ½Çºñ±³ÃøÁ¤)
|
16.8
gr/m2 ( Áß·®¼Õ½Ç )
|
167.4
gr/m2 ( Áß·®¼Õ½Ç ) |
SABS
Test Method 155, ½ÃÆíÀ» ¿°¼öºÐ¹« 400 ½Ã°£ ÈÄ m2 ·Î ȯ»êÇÏ¿© Áß·® ¼Õ½Ç ÃøÁ¤ |
¿°¼öºÐ¹«½ÃÇè
Å×½ºÆ® (National Cheng Kung University, Taiwan)
|
4500
½Ã°£ ÈÄ¿¡µµ ³ì¹ß»ý ¹«
|
172
½Ã°£ ÈÄ ³ì¹ß»ý |
ASTM
B117-94, ¿ëÀ¶¾Æ¿¬µµ±Ý ½ÃÆí°ú Zinga 120 ¥ìm µµÆ÷ ½ÃÆí ¹× ¿ëÀ¶¾Æ¿¬µµ±Ý¸éÀ§¿¡ Zinga
60 ¥ì µµÆ÷½ÃÆí ºñ±³ |
»ê¿ë¾×¿¡¼ÀÇ
³»ºÎ½Ä¼º BNF Fulmer, UK(ºÎ½ÄÁøÇà¼Óµµ ÃøÁ¤)
|
0.035
mm / year
|
0.11
mm / year |
pH
6.0 ¡¾ 0.2 ¿ë¾× ( 0.01 Molar Sulphate + ¿°È³ªÆ®·ý ) |
¾ËÄ®¸®¿¡¼ÀÇ
³»ºÎ½Ä¼º
³²¾Æ°ø Van Reef ±Ý±¤
|
5
³â ÈÄ¿¡µµ ³ì¹ß»ý ¹«
|
6
°³¿ù ÈÄ ³ì ¹ß»ý |
pH
11.5 ÀÇ °»³»¼ö ¿ë¾× ( Water Pump ¿¡ µµÆ÷ ) |
¾Æ¿¬ÀÇ
¼øµµ
|
99.995
%
|
98
% |
¾Æ¿¬ÀÇ
ÇÔ·®
|
96
%
|
80
- 85 % (ö-
¾Æ¿¬ ÇÕ±ÝÃþ Æ÷ÇÔ) |
pH
¹üÀ§
|
3
¢¦ 11
|
5
¢¦ 9 |
ÇǸ·ÀÇ
À¯¿¬¼º
|
À¯¿¬
( Flexible )
|
¾Æ¿¬µµ±ÝÃþ
¾Æ·¡ Çձݻý¼º À¸·Î ÇǸ·ÃþÀÌ °æÁú |
Å©·¢
¹ß»ý °¡´É¼º
|
¹«
|
½Ã°£
°æ°úÇÒ¼ö·Ï Ä¿Áü |
Ãæ°ÝÈí¼ö¼º
(Compressibility)
|
¿ì¼ö
|
Ã뼺ÀÌ
ÀÖÀ½ |
¿ÜºÎÀÇ
Ãæ°Ý¿¡ ÀÇÇÑ ÇǸ·¼Õ»ó¿©ºÎ |
ÀÛ¾÷¹°ÀÇ
º¯Çü
|
»ó¿ÂµµÆ÷À̹ǷÎ
º¯Çü ¹«
|
¿¿¡
ÀÇÇÑ Çü»óÀÇ º¯Çü °¡´É |
ÀÌÁ¾
º¹ÇÕÀçÁúÀÇ Ã³¸®½Ã ¿Ü°üÀÇ º¯È
|
¹«
|
Â÷À̰¡
³¯ ¼ö ÀÖÀ½ |
ÀÌÁ¾
ÀçÁúÀÇ ÀÛ¾÷¹°ÀÇ Ã³¸®½Ã ¿Ü°üÀÇ Â÷ÀÌ |
ÀÌÁ¾
º¹ÇÕÀçÁúÀÇ
󸮽à ±Ý¼ÓÁ¶Á÷ÀÇ
º¯È
|
¹«
|
Â÷À̰¡
³¯ ¼ö ÀÖÀ½ |
ÀÌÁ¾
ÀçÁúÀÇ ÀÛ¾÷¹°ÀÇ Ã³¸®½Ã Á¶Á÷ÀÇ º¯È |
Ç¥¸éó¸®
¿ä°Ç
|
»÷µåºê¶ó½ºÆ®°¡
¹Ýµå½Ã ÇÊ¿äÇÏÁö´Â ¾ÊÀ½
|
¾ö°Ý
- SIS Sa 3
Pickling, Passivating |
ÀÛ¾÷¹°
Ç¥¸éÀÇ ³ì
|
Çæ°Å¿î
³ì¸¸ Á¦°Å ÈÄ µµÆ÷°¡´É
|
³ì
¿ÏÀü Á¦°Å |
Ç¥¸éÀÇ
½À±â
|
½À±â
À§¿¡ µµÆ÷°¡´É
|
¿ÏÀü
°ÇÁ¶ Ç¥¸é |
ÇöÀå
µµÆ÷ °¡´É¼º
|
ÇöÀå
µµÆ÷, shop µµÆ÷
|
shop
µµÆ÷ |
º¸¼ö
°¡´É¼º
|
öºê·¯½Ã
ÈÄ ½±°Ô º¸¼ö
|
º¸¼ö
°ÅÀÇ ºÒ°¡ |
ÀçµµÆ÷
|
Zinga
ÇǸ· À§¿¡ ÀçµµÆ÷ ¿ëÀÌ
( Zinc Salt µî ¹°¼¼Ã´ ÈÄ )
|
Àçó¸®
ºÒ°¡ |
»óµµÀÇ
µµÆ÷
|
Zinga
À§¿¡ »óµµ Á÷Á¢µµÆ÷ °¡´É
|
»óµµµµÆ÷½Ã
Áßµµ ÇÊ¿ä |
 |
¿ëÀ¶¾Æ¿¬µµ±Ý°ú
°ü·ÃµÈ ¹®Á¦Á¡
¼³°è´ã´ç ¿£Áö´Ï¾îµéÀº ¿ëÀ¶¾Æ¿¬µµ±Ý°ú °ü·ÃÇÏ¿© µµ±Ý ÈÄ¿¡ ¹ß»ýÇÒ ¿ì·Á°¡ ÀÖ´Â ¹®Á¦Á¡°ú À§Çè¿ä¼Ò¸¦ °¨¾ÈÇÏ¿©¾ß Çϸç,
ö¹°ÀÇ ¼³°è¸¦ ÀÌ¿¡ µû¶ó ÇÏ¿©¾ß ÇÕ´Ï´Ù.
¸ðµç Á¾·ùÀÇ ±Ý¼ÓÀÌ ¾Æ¹«·± ¹®Á¦¾øÀÌ ( ¿ëÀ¶¾Æ¿¬ µµ±ÝÀÌ 450 ¡É ÀÇ °í¿ÂÀ¸·Î 󸮵DZ⠶§¹®¿¡ ) ¿ëÀ¶¾Æ¿¬µµ±ÝÀ¸·Î
ó¸®µÉ ¼ö ÀÖ´Â °ÍÀº ¾Æ´Õ´Ï´Ù. ¿ëÀ¶¾Æ¿¬µµ±ÝÀ» Çϱâ Àü¿¡ ½Ç¸®ÄÜ ÇÔ·® µî ±Ý¼ÓÀÇ ±¸¼º¼ººÐ¿¡ ´ëÇÑ ¾î´À Á¤µµÀÇ
ÀÌÇØ°¡ ÇÊ¿äÇÕ´Ï´Ù. ¼·Î ´Ù¸¥ ÀÌÁ¾ÀÇ ±Ý¼ÓÀÌ °áÇÕµÈ ±¸Á¶¹°ÀÇ °æ¿ì ´õ¿í ¹®Á¦°¡ ¹ß»ýÇÒ ¼ÒÁö°¡ Å®´Ï´Ù.
450 ¡É ÀÇ °í¿Â¿¡¼ ¿ëÀ¶¾Æ¿¬¿¡ ±Ý¼ÓÀ» ÇÔħÇÑ °æ¿ì ±Ý¼ÓÀÌ °¡½º¸¦ ÀûÀýÈ÷ ¹æÃâÇÏÁö ¸øÇÏ¸é ¸Å¿ì À§ÇèÇÑ
Æø¹ßÀÌ ÀϾ ¼ö ÀÖ½À´Ï´Ù. ( ½ÇÁ¦·Î µ¶ÀÏ¿¡¼ Æø¹ß »ç·Ê°¡ ÀÖÀ½ ) ÇÔħ Àü¿¡ µå¸±·Î °¡½º¹æÃâ ±¸¸ÛÀ»
¸¸µé¾î ÁÖ¾î¾ß ÇÕ´Ï´Ù.
ÇϳªÀÇ ±¸Á¶¹°¿¡ ¿©·¯ °¡Áö ±Ý¼ÓÀÌ »ç¿ëµÇ¾îÁø´Ù´Â °ÍÀ» °¨¾ÈÇÒ ¶§ µµ±Ý ÈÄ °¢ ´Ù¸¥ ¼ººÐÀÇ ±Ý¼Ó¸¶´Ù ¿Ü°üÀÌ
´Þ¸® º¸ÀÏ ¼ö ÀÖ´Ù´Â Á¡µµ °¨¾ÈÇÏ¿©¾ß ÇÕ´Ï´Ù.
¿ëÀ¶¾Æ¿¬µµ±ÝÀÇ ÇǸ·µÎ²²´Â °æ¿ì¿¡ µû¶ó 30 - 200 % ÀÇ ÆíÂ÷¸¦ º¸ÀÌ´Â ¼ö°¡ Á¾Á¾ ÀÖÀ¸¸ç, ¶§·Î´Â
¼ÒÀ§ ¡°nose" Çö»óÀÌ ¹ß»ýÇϴµ¥ ÀÌ´Â ½Ã°£°ú ºñ¿ëÀ» µé¿© ¼ÕÀ¸·Î ÀÏÀÏÀÌ Á¦°ÅÇØ¾ß ÇÕ´Ï´Ù.
±Ý¼ÓÀ» ÇÔħ ÀÌÀü¿¡ ÀûÀýÈ÷ ¿¹¿À» ÇÏÁö ¾ÊÀ¸¸é ¾î¶² Á¾·ùÀÇ ±Ý¼ÓÀ̳ª Çü»óÀÇ ÀÛ¾÷¹°Àº ÇÔħ Áß ¼Õ»óÀ» ÀÔÀ»
¼ö ÀÖ½À´Ï´Ù. ¼·Î ´Ù¸¥ ¿ÆØÃ¢¼ºÀ¸·Î ÀÎÇÏ¿© ±Ý¼Ó¿¡ Å©·¢ÀÌ ¹ß»ýÇÒ ¼öµµ ÀÖÀ¸¸ç, ÀÌ·¯ÇÑ Å©·¢Àº ÃÊÀ½ÆÄ·Î¸¸
ŽÁö°¡ °¡´ÉÇÕ´Ï´Ù. ( µ¶ÀÏ¿¡¼´Â ÀÌ·¯ÇÑ Å©·¢ ¹ß»ýÀ¸·Î ÀÎÇÏ¿© ¼ö¹é¸¸ ¸¶¸£Å©ÀÇ ¼Õ½ÇÀ» ÀÔÀº »ç·Ê°¡ ÀÖ½À´Ï´Ù.
Ưº°ÇÑ °æÇèÀ» ÇÑ ÀÌ °í°´Àº ÀÌ »ç°í ÀÌÈÄ·Î Zinga ¸¦ »ç¿ëÇϰí Àִµ¥ º°´Ù¸¥ È«º¸¸¦ ÇÊ¿ä·Î ÇÏÁö ¾Ê¾Ò½À´Ï´Ù.
)
3 mm ÀÌÇÏÀÇ Æ¯È÷ ¾ãÀº µÎ²²ÀÇ ÀÛ¾÷¹°Àº ÇÔħ Áß¿¡ º¯ÇüÀÌ ¿Ã °¡´É¼ºÀÌ ¸Å¿ì Å®´Ï´Ù. ½ÉÁö¾î´Â ÀϺÎÀÇ
º¯ÇüÀ¸·Î ÀÎÇÏ¿© ÀüüÀÇ ÀÛ¾÷¹°À» »ç¿ëÇÒ ¼ö ¾ø°Ô µÇ´Â »ç·Êµµ ÀÖ½À´Ï´Ù. ÀÌ´Â ºñ¿ë°ú Á÷°áµÇ´Â ¹®Á¦ÀÔ´Ï´Ù.
ÀÛ¾÷¹°ÀÌ Å©°Å³ª ±ä °æ¿ì¿¡´Â ºÐ¸®ÇÏ¿© ÀÛ¾÷À» ÇÏ°í ´Ù½Ã ¿ëÁ¢Çϰųª ¿ëÀ¶Á¶°¡ ÀÖ´Â ÇöÀåÀ¸·Î ¿î¼ÛÇÏ´Â µîÀÇ
ºÒÆíÀÌ ÀÖ¾î ÀΰǺñ, ¿î¼Ûºñ, ½Ã°£ µîÀÇ Ãß°¡ºñ¿ë ¹ß»ý¿äÀÎÀÌ µû¸¨´Ï´Ù.
½À±â°¡ ÀÖ´Â °÷¿¡ ¿ëÀ¶¾Æ¿¬µµ±ÝÀÌ µÈ ÀÛ¾÷¹°À» ³õ¾ÆµÎ¸é À̸¥¹Ù ¡°¹é³ì (white rust)"
°¡ ¹ß»ýÇÒ ¿ì·Á°¡ ³ô½À´Ï´Ù. »ç¿ëÀÚ¿¡ µû¶ó¼´Â ÀÌ·Î ÀÎÇÑ ¿Ü°üÀ» ¹®Á¦»ï°Ô µË´Ï´Ù.
¿ëÀ¶¾Æ¿¬µµ±Ý¸é À§¿¡ »óµµ¸¦ µµÆ÷ÇÏ´Â °æ¿ì¿¡´Â Ç¥¸é󸮿¡ Ưº°ÇÑ ÁÖÀǸ¦ ÇÏ¿©¾ß ÇÏ¸ç ºÒÃæºÐÇÑ Ç¥¸é󸮴Â
ÆäÀÎÆ®ÀÇ Á¢ÂøºÒ·®À» °¡Á®¿À°Ô µË´Ï´Ù.
|