

°³¿ä

- ¾Æ¿¬¼ººÐÀÇ °¥¹Ù´Ï Àü±â ¹æ½Ä¿¡ ÀÇÇÑ Ã¶Á¦ÀÇ ºÎ½Ä¹æÁö ÄÚÆÃÁ¦ ( °ÇÁ¶ ÈÄ ¾Æ¿¬ ÇÔ·® 92 % )
- źȼö¼Ò¹° ( Hydrocarbon ) ÀÌ µé¾îÀÖÁö ¾ÊÀº ( 0 % ) ¼ö¿ë¼º Zinc Silicate
- 2¾×Çü ¹«±âÄÚÆÃÁ¦·Î¼ ¿¾ÇÇÑ »ê¾÷ȯ°æ¿¡ »ç¿ëÇÒ ¼ö ÀÖ°í »ç¿ëÀÚ°¡ ¾ÈÀüÇÏ°Ô »ç¿ëÇÒ¼ö ÀÖÀ½

È¿´É

- ´ë±âºÐÀ§±â, ¿°±â°¡ ÀÖ´Â °÷, ½À±â°¡ ÀÖ´Â °÷, ±âü»óÀÇ ºÎ½Ä¼º ÈÇй°Áú¿¡ ÀÇÇÑ
ºÎ½Ä¿¡ ´ëÇÏ¿© ¿ÏÀüÇϰí
³»±¸¼ºÀÖ´Â ³»ºÎ½Ä¼º´ÉÀ» ¹ßÈÖ
BelgiumFlotreac
»çÀÇ ³¹æ¼³ºñ Áß ¼®Åº°ø±Þ¼³ºñ - 1985 ³â ¼®Åº°ø±Þ È£ÆÛ ³»¿ÜºÎ¿¡
Aquazinga
µµÆ÷, 15³â ÈÄ À¯Áöº¸¼ö±â°£Áß °Ë»ç°á°ú 100 % ¹«°áÇÔ (2000 ³â 9 ¿ù »çÁø)

- źȼö¼Ò¹°Áú ( hydrocarbons ) À̳ª À¯±â¿ëÁ¦ Èñ¼®Àç, ¶Ç´Â ¸î¸îÀÇ ÈÇй°ÁúÀÌ µé¾îÀÖ´Â
( pH 5.5
- 10.5 ) ¹°, ´ëÀüÀÌ µÈ ¹° ( charged water ), ÇØ¼ö ( Ç׽à ħ¼öºÎÀ§ Æ÷ÇÔ ) ¿Í Á¢
ÃËÇÏ´Â ºÐÀ§±â¿¡¼
¿ÏÀüÇÏ°í ±ØÈ÷ ³»±¸¼ºÀÖ´Â ³»ºÎ½Ä¼º´ÉÀ» ¹ßÈÖ

- °è¼Ó °í¿Â¿¡ Á¢ÃËÇÏ´Â ºÎÀ§, ¹Ýº¹ÀûÀÎ ¿Ãæ°ÝÀÌ ÀÖ´Â °í¿ÂºÎÀ§¿¡¼ ( 600 ¡É ) ¿¡¼ ¿ì¼öÇÑ ³»¿¼º.
À§ÀÇ °í¿Â¿¡¼ ÇØ¼ö, ´ã¼ö, 󸮼ö ( treated water ) ¿Í Á¢ÃËÇÑ ºÎÀ§, ²ú´Â źȼö
¼Ò¹°Áú¿¡ Á¢ÃËÇÑ
ºÎÀ§¿¡¼ ¿ì¼öÇÑ ³»¿¼º.½ºÆÀÀ̳ª °¡½º ¹× À̵éÀ» ½îÀÌ´Â ºÎÀ§¿¡¼ ¿ì¼öÇÑ
¼º´É

- ÀÌÀü¿¡ ¾Æ¿¬ÇǸ·ÀÌ Ã³¸®µÈ öÁ¦Ç¥¸é À§¿¡ »ç¿ë °¡´É ( Á¦Á¶ÀÚÀÇ »ç¿ë¼³¸í¼ ÂüÁ¶ )

- ¾çÈ£ÇÑ ¿Àüµµ¼º ¹× ¿ÏÀüÇÑ µîÀüÀ§¼º ( perfect equi-potentiality ), Cathodic
protection
( Èñ»ýºÎ½Ä¿¡ ÀÇÇÑ
±âÀ纸ȣ ) ÇǸ·°ú °°ÀÌ »ç¿ëÇϸé, Aqua-Zinga ÇǸ·ÀÌ ÀÚµ¿À¸·Î Èñ»ý
ºÎ½Ä±â´ÉÀ» °è½ÂÇϹǷÎ
¿Ïº®ÇÑ ºÎ½Ä¹æÁö ¼º´É¹ßÈÖ

- Anti-Foul ±â´É, ÇØ¾ç¿À¿°¹°Áú¿¡ ¿À¿°µÇ´Â ¼³ºñÀÇ Ã»¼Ò ¸Å¿ì ¿ëÀÌ
- ¿ëÁ¢ Àü ¸Å¿ì Ź¿ùÇÑ ÇÁ¶óÀ̸Ó, Aqua-Zinga °¡ ó¸®µÈ ±Ý¼Ó³¢¸®µµ ¿ëÁ¢ °¡´É
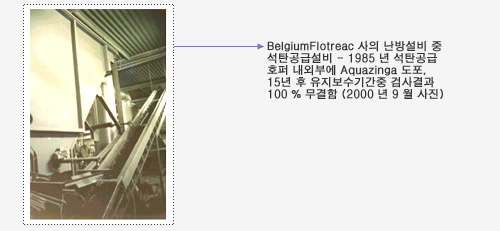
ÀÌÁ¡

- ´Ù¸¥ ´ëºÎºÐÀÇ ÄÚÆÃÁ¦¿Í´Â ´Þ¸® µµÆ÷½Ã ÁÖº¯¿Âµµ¿¡ ¿µÇâÀ» ¹ÞÁö ¾ÊÀ½. ( 5¡É ÀÌ»ó)
- ¼³ºñÀÇ °¡µ¿ ÁßÁö ½Ã°£À» ÃÖ¼ÒÈÇÏ´Â ½Å¼ÓÇÑ °æÈ½Ã°£
- ¹«Çؼº ¾ÈÀü¼º - ¹ÙÀδõ ¼ººÐÀº 100 % ¹«±âÁú·Î¼ ¼ö¼ºÀ¸·Î ÀÎȼºÀÌ ¾ø°í, ¿À¿°À» À¯¹ß
ÇÏÁö ¾ÊÀ¸¸ç, °¡½º°¡
¹æÃâµÇÁö ¾Ê°í, µ¶¼ºÀÌ ¾ø°í, ÇǺξ˷¹¸£±â¸¦ À¯¹ßÇÏÁö ¾Ê°í, 2 ¾×Çü
À¸·Î Àå±âº¸°üÀÌ
°¡´É.
Ư¼º
( Technical Characteristics )

- Á¦Ç°¼ººÐ : Belgium Flotreac »çÀÇ ³¹æ¼³ºñ Áß
¼®Åº°ø±ÞÈ£ÆÛ
1985 ³â ³»¿ÜºÎ¿¡
AquaZinga µµÆ÷
¹ÙÀδõ ; 100
% ¹«±âÁú·Î¼ ¼ö¼ºÀÇ °í±â¼ú °³³äÀÇ ¹ÙÀδ٠»ç¿ë ( ºñÁß 1.18 )
Pigment
; ¸Å¿ì °í¹Ðµµ °í¼øµµ ¾Æ¿¬¸» ( ºñÁß 7.14 )
- ¹°¸®Àû Ư¼º :

ºñÁß ; 2.72
( ¡¾0.05) g/cm3
°íÇü¹°ÁúÇÔ·® :
75.6 % - Áß·®ºñ
38.0 % -
ºÎÇǺñ
ÀÌ·Ð»ó µµÆ÷À²
; 3.5 m2 / kg
°ÇÁ¶½Ã°£ : (
¿Âµµ ¹× ½Àµµ¿¡ µû¶ó ´Ù¸§ )
ÁöÃ˰ÇÁ¶ - ¡¾
15 ºÐ ( 20 ¡É )
ÀçµµÀå - 24
½Ã°£ ÈÄ
°ÇÁ¶ÇǸ· ( ¸Å²ô·¯¿î
ȸ»ö ÇѰ¡Áö »ö»ó ) ;
1 ȸ µµÀå¿¡
40 micron
99.995 %
¼øµµÀÇ ¾Æ¿¬ÇÔ·® 92 %
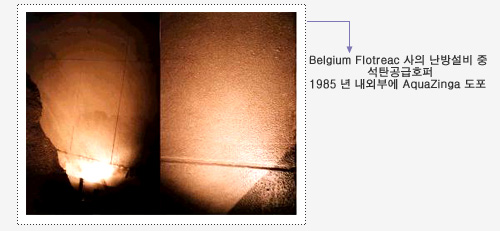
»ç¿ë»óÀÇ
Àý´ëÀû ¾ÈÀü¼º ;

(A) Powder
: ¹°°ú Á¢Ã˽à ºñÀÎȼº °¡½º ¹æÃâ
(B) ¹ÙÀδÙ
: 100 % ¹«±âÁúÀÇ ¼ö¿ë¾× - ¿À¿°¼º Àü¹«, ºñÀÎȼº, °¡½º¹ß»ê ¹«
È¥ÇÕ ÈÄ :
°¡½º¹ß»ê ¹«, ¹«µ¶¼º, ¾Ë·¹¸£±â À¯¹ß ¹«, ¿ë±â ³» ÀÛ¾÷ µî Æó¼âÀå¼Ò ÀÛ¾÷¿¡ ¸Å¿ì
ÀûÇÕ
Ç¥ÁØÆ÷Àå
;

5 kg Kit
; 3.5 kg powder ¿Í 1.5 kg ¹ÙÀδÙ
10 kg Kit
; 7.0 kg powder ¿Í 3.0 kg ¹ÙÀδÙ
25 kg Kit
; 17.5 kg powder ¿Í 7.5 kg ¹ÙÀδÙ
º¸°ü
;

º¸°üÀÇ ¿ëÀÌ
; ¿ÀÌ ÀÖ´Â °÷ ¹× ½ÀÇÑ Àå¼Ò¸¦ ÇÇÇÒ °Í
±ä º¸°ü±â°£
; 18 °³¿ù ÀÌ»ó, ¹ÙÀδٰ¡ ¾ó¾îµµ Á¦Ç° ¼º´É ¿µÇâ ¹«
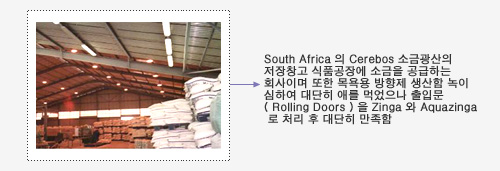
±Ý¼ÓÀÇ
Ç¥¸éó¸®

¹Ýµå½Ã »÷µåºê¶ó½ºÆ®¸¦
¿äÇÔ ( ¿ÀÀϰú °°Àº ¿À¿°¹°Áú ¹× ½À±â°¡ ¾ø´Â °ø±â »ç¿ë )
Ç¥¸éÀÇ ¿äöÀº
RA12.5 ±âÁØ Sa 3 ¿ä¸Á ( Sa 2.5 µµ °æ¿ì¿¡ µû¶ó °¡ÇÔ )
Ç¥¸éó¸®ÇÑ ±Ý¼Ó¸é¿¡ÀÇ
1 Â÷ µµÆ÷
Ç¥¸éó¸® ÈÄ µÇµµ·Ï
»¡¸® µµÆ÷ ¿ä¸Á ( ½Àµµ°¡ ÀÖ´Â °æ¿ì ÃÖ´ë 1 ½Ã°£ À̳», °ÇÁ¶ÇÑ ³¯¾¾ÀÎ
¿ì ÃÖ´ë 5 ½Ã°£
À̳» )
µµÆ÷Àåºñ

º×À¸·Î µµÆ÷°¡´É
( »õ º× »ç¿ë )
µÇµµ·Ï Àú¾Ð ½ºÇÁ·¹À̸¸À»
»ç¿ëÇÏ¿© ( °ø¾Ð °Ç »ç¿ë ) Èñ¼®ÇÏÁö ¾Ê°í µµÆ÷ÇÒ °Í
ÇǸ·µÎ²²´Â ³Ê¹«
µÎ²®°Ô ÇÏÁö ¸»°í ÀûÀýÇÑ µÎ²²·Î µµÆ÷ÇÒ °Í
°ø¾Ð °Ç ; »õ
°ÍÀ» »ç¿ëÇϰųª ¿ÀÀÏÀ» Á¦°ÅÇÑ ±ú²ýÇÑ °Ç »ç¿ë
Àåºñ¼¼Ã´

º×ÀÛ¾÷ ÈÄ µÇµµ·Ï
»¡¸® ¹°¸¸ »ç¿ëÇÏ¿© ¼¼Ã´ÇÒ °Í
¼¼Ã´ ÈÄ Àåºñ
Àç»ç¿ë °¡´É
ÀÚÀçÈ¥ÇÕ

¹ÙÀδ٠¼ººÐÀ»
Àß ÀúÀº ÈÄ powder ¸¦ ¼¼È÷ ºÎÀ¸¸ç Àú¾îÁÝ´Ï´Ù. ±ÕÀÏÇÑ »ö»óÀÌ ³¯ ¶§±îÁö
Á£½À´Ï´Ù.
±ú²ýÇÑ ¹Í¼¸¦
»ç¿ëÇϰí powder °¡ ¹¶Ä£ ºÎºÐÀÌ ¾øµµ·Ï ÁÖÀÇÇÕ´Ï´Ù. )
½ºÇÁ·¹ÀÌ °ÇÀ»
»ç¿ëÇÏ¿© µµÆ÷ÇÒ ¶§´Â µÎ ¼ººÐÀÌ È¥ÇÕµÈ µÚ Filtering ÇÏ¿© µµÆ÷ÇÏ´Â
°ÍÀÌ ÁÁ½À´Ï´Ù.
È¥ÇÕÇÑ ÀÚÀç´Â
¼÷¼º½Ã°£ÀÌ ÇÊ¿ä¾øÀ¸¹Ç·Î °ð¹Ù·Î µµÆ÷ÇÏ¸é µË´Ï´Ù.
¹ÙÀδٿ¡ ºñÇØ
¾Æ¿¬¸»ÀÇ ºñÁßÀÌ ³ôÀ¸¹Ç·Î È¥ÇÕµÈ ÀÚÀç°¡ ±ÕÀÏÇÏ°Ô ÇÏ·Á¸é µµÆ÷Áß¿¡µµ
°è¼Ó Àú¾îÁÖ´Â
°ÍÀÌ ÇÊ¿äÇÕ´Ï´Ù.
Èñ¼®

Á¦Ç°Àº È¥ÇÕ ÈÄ
±×´ë·Î µµÆ÷ÇÏ°Ô µÇ¾î ÀÖÀ¸¹Ç·Î º¸Åë Èñ¼®Àº ÇÊ¿ä¾ø½À´Ï´Ù.
Èñ¼®À» ÇÏ·Á¸é
Á¦Á¶ÀÚ³ª ´ë¸®Á¡¿¡ ¹®ÀÇ ÈÄ ±ú²ýÇÑ ¹°À» ÃÖ´ë 3 - 5 % ÇÒ ¼ö ÀÖ½À´Ï´Ù. ( ÀÚµ¿
Èñ¼®±â´Â »ç¿ëÇÏÁö
¸¶½Ê½Ã¿À )
°¡»ç½Ã°£

6 ½Ã°£ ( ¿Âµµ¿¡
µû¶ó ´Ù¸§ )
µµÆ÷½Ã
ÁÖº¯¿©°Ç

¸¼Àº ³¯, ÅëdzÀÌ
Àß µÇ´Â °÷
ÁöÃ˰ÇÁ¶
( Dry to the Touch )

15 - 30
ºÐ, µû¶æÇÑ ±Ý¼ÓÇ¥¸é¿¡¼´Â ÁöÃ˰ÇÁ¶°¡ ´õ ºü¸§.
¿Âµµ°¡ ³·°í
½Àµµ°¡ ³ôÀ¸¸é ÁöÃ˰ÇÁ¶½Ã°£ÀÌ ±æ¾îÁü. ( ±æ¾îµµ 7 ½Ã°£À̸é ÁöÃ˰ÇÁ¶°¡ µÊ )
¶ß°Å¿î
³¯¾¾¿¡¼ÀÇ µµÆ÷ÀÛ¾÷

¶ß°Å¿î Á÷»ç±¤¼±À»
¹Þ´Â °÷¿¡¼ ÀÛ¾÷À» ÇѴٰųª ÇÏ¸é ±Þ¼ÓÇÑ °ÇÁ¶·Î ÀÎÇÏ¿© ƯÈ÷ ÄڳʺÎ
À§³ª Æ¢¾î³ª¿Â
ºÎÀ§¿¡ ÀÛÀº Å©·¢ÀÌ ¹ß»ýÇÒ ¼ö ÀÖÀ½. ±×·¯³ª ÀÌ·¯ÇÑ Å©·¢Àº ÄÚÆÃ¸·ÀÇ ¼º´É¿¡
¿µÇâÀ» ÁÖÁö ¾ÊÀ½.
öºê·¯½Ã·Î ÄÚÆÃÇ¥¸éÀ» ¾µ¾îÁÖ¸é µÇ¸ç Ãß°¡ÇǸ·À» ¿Ã¸± Çʿ䰡 ¾øÀ½.
±×·¯³ª ÀÌ·¯ÇÑ
ºÒÆíÀ» ´ú±â À§Çؼ´Â ÀÛ¾÷Àå¼Ò¸¦ Á÷»ç±¤¼±À» Â÷´ÜÇϰí ÀÛ¾÷ÇÏ´Â °ÍÀÌ ÁÁÀ½
ÁÖ) ¶ß°Å¿î Á¶°Ç¿¡¼
ÀÛ¾÷Çϸé ÇǸ·µÎ²²°¡ »ó´çÈ÷ µÎ²¨¿öÁö¹Ç·Î ÀÚÀçÀÇ ¼Ò¸ð°¡ ¸¹¾ÆÁý´Ï´Ù.
½Àµµ°¡
¸Å¿ì ³ôÀº ¿©°Ç¿¡¼ÀÇ µµÆ÷

µµÆ÷µÈ Á¥Àº ÇǸ·ÀÌ
¸¶¸£Áö ¾ÊÀ» Á¤µµÀÏ °æ¿ì¿¡´Â ¿Ç³±â µîÀ» ÀÌ¿ëÇÏ¿© °ÇÁ¶½Ã°£À» ´ÜÃà½Ã
ų ¼ö ÀÖ½À´Ï´Ù.
¿Ç³±â´Â ¿À»
½î´Â ¹æÇâÀ» Àß Á¶ÀýÇØ¾ß Çϸç ÇÁ·ÎÆÇ°¡½º µîÀÇ Ã»Á¤¿¬·á¸¦ »ç¿ëÇÏ¿© ¿¬±â
°¡ ³ªÁö ¾Êµµ·Ï
ÇØ¾ß ÇÕ´Ï´Ù.
°á·Î°¡
Àִ ǥ¸é

ÇÏÀý±â¿¡ ¿Âµµ°¡
±Þ¼ÓÈ÷ ¶³¾îÁö¸é ±Ý¼ÓÇ¥¸é¿¡ °á·Î°¡ »ý±æ ¿ì·Á°¡ ÀÖÀ¸¹Ç·Î ÁÖÀÇÇØ¾ß
ÇÕ´Ï´Ù. (
°á·Î´Â À°¾ÈÀ¸·Î´Â °üÂûÇÏ±â ¾î·Æ½À´Ï´Ù. )
°Á¦°ÇÁ¶

»óµµ¸¦ µµÆ÷ÇϰíÀÚ
°ÇÁ¶¸¦ »¡¸® ÇϰíÀÚ ÇÏ´Â °æ¿ì¿¡´Â ±âÀçÀÇ Ç¥¸éó¸® ÀüÈÄ¿¡ ±Ý¼Ó
Ç¥¸éÀ» µ¤¿©ÁÖ°í
´õ¿î ±Ý¼Ó¸é¿¡ µµÆ÷ÇÏ¸é °ÇÁ¶°¡ »¡¶óÁý´Ï´Ù.
ÀÛÀº ÀÛ¾÷¹°À̶ó¸é
°ÇÁ¶·Î¿¡ ³Ö¾î °ÇÁ¶½Ãų ¼ö ÀÖ½À´Ï´Ù.
Ç¥¸é
ó¸®µÈ ¸éÀÇ ¿À¿°ºÎÀ§

ÀÛ¾÷¹°ÀÇ Ãë±ÞÁß¿¡
ºÎÁÖÀÇ·Î µµÆ÷ÇÒ Ç¥¸é¿¡ ±×¸®½º µîÀÌ ¹¯Àº °æ¿ì¿¡´Â À¯±â¿ëÁ¦ µîÀ¸·Î
´ÛÀ» ÇÊ¿ä¾øÀÌ
ÅäÄ¡ ºÒ µîÀ¸·Î ºÒ¼ø¹°À» Å¿ö ¾ø¾Ö¸é µË´Ï´Ù. Á¦°Å ÈÄ Ç¥¸éÀÌ ½Ä±â¸¦
±â´Ù·Á µµÆ÷ÇÕ´Ï´Ù.
Àå½Ã°£
ÀÛ¾÷Áß´Ü ÈÄ ÀÛ¾÷ Àç°³

±âÈÄ µîÀÇ ¿©°ÇÀ¸·Î
ÀÎÇÏ¿© ¿À·£ ½Ã°£ ÀÛ¾÷À» Áß´ÜÇÏ¿´À» °æ¿ì ÀÛ¾÷ Àç°³ Àü¿¡ Ç¥¸é¿¡
À̹°ÁúÀÌ ¹¯¾úÀ¸¸é
Á¦°ÅÇϰí ÃæºÐÈ÷ ¼¼Ã´ÇÑ ÈÄ µµÆ÷ÇØ¾ß ÇÕ´Ï´Ù. 24 ½Ã°£ ¸¶¸£±â¸¦
±â´Ù·Á ´ÙÀ½
µµÆ÷ÀÛ¾÷À» ½ÃÀÛÇÕ´Ï´Ù.
ÇǸ·
À§¿¡ ÇϾá ÈçÀûÀÌ ¹ß»ýÇÏ´Â °æ¿ì

ÄÚÆÃ ÈÄ ¹ã¿¡
°á·Î°¡ »ý±â¸é ÇǸ· À§¿¡ ÇÏ¾á ¶ì°¡ ¹ß»ýÇÕ´Ï´Ù. ÀÌ·¯ÇÑ Çö»óÀº °ÇÁ¶ÇÑ ³¯
³·¿¡ ÀÛ¾÷ ÈÄ¿¡
´ëºÎºÐ ¹ß»ýÇϴµ¥ ¿ÏÀüÈ÷ ´Û¾Æ³»°Å³ª ¹°·Î ¼¼Ã´ÇÏ¸é ¾ø¾îÁý´Ï´Ù.
ÁÖ) ÇÏ¾á ¶ì°¡
¹ß»ýÇÏ´Â °ÍÀº ¿°·ÁÇÒ Çʿ䰡 ¾ø½À´Ï´Ù. µµÆ÷°¡ ¿Ïº®È÷ Àß µÈ Áõ°ÅÀÔ´Ï´Ù.
Aqua-Zinga
ÀÇ ÀçµµÆ÷

ÁöÃ˰ÇÁ¶°¡ µÇ¸é
°ð¹Ù·Î 2 Â÷ µµÆ÷¸¦ ÇÒ ¼ö ÀÖ½À´Ï´Ù.
¾î¶»µç ÄÚÆÃÀÛ¾÷
Áß°£¿¡ ¿¬±â, ¹è±â°¡½º, ¶Ç´Â ¸ÕÁö°¡ ÀÌÀü ÀÛ¾÷ÇÑ ÇǸ· À§¿¡ ¹¯¾î ¿À¿°
µÇÁö ¾Êµµ·Ï
ÁߴܾøÀÌ ÀÛ¾÷ÇÏ´Â °ÍÀÌ ÁÁ½À´Ï´Ù. ÀÌÀüÀÇ ÄÚÆÃÃþÀÌ °ÇÁ¶°¡ µÈ ÈÄ ÀÛ¾÷ÇØ¾ß
ÇÏ´Â °ÍÀº ¹°·ÐÀÔ´Ï´Ù.
µµÆ÷ȸ¼ö

º¸Åë 2 ȸ
ÄÚÆÃÀ¸·Î Á·ÇÕ´Ï´Ù. °¢ °æ¿ì¿¡ µû¶ó Á¦Á¶ÀÚ ¹× ´ë¸®Á¡ÀÇ Áö½Ã¿¡ µû¶ó µµÆ÷ȸ¼ö¸¦ °áÁ¤ÇÏ¿©¾ß
ÇÕ´Ï´Ù. ¶§·Î´Â 1 ȸ µµÆ÷·Î ÃæºÐÇÑ °æ¿ìµµ ÀÖ°í 4 - 5 ȸ µµÆ÷°¡ ¿ä±¸µÇ´Â
°æ¿ìµµ ÀÖ½À´Ï´Ù.
ÁÖ) ´ëºÎºÐ
³Ê¹« µÎ²®°Ô µµÆ÷Çϸé ÁÁÁö ¾Ê½À´Ï´Ù.
´Ù¸¥
»óµµÀÇ µµÆ÷

Á¦Á¶ÀÚÀÇ ¹×
´ë¸®Á¡ÀÇ Áö½Ã¸¦ ¹Þ°í µµÆ÷ÇϽʽÿÀ
°æÈ½Ã°£
( »óµµ¾øÀÌ »ç¿ëÇÏ´Â °æ¿ì )

°í¿ÂºÎÀ§/½À±â
ÀÖ´Â ºÎÀ§ ; ÃÖ¼Ò 24 ½Ã°£
´ã¼ö/ÇØ¼ö ;
ÃÖ¼Ò 48 ½Ã°£
|